Feature overview
In the list below all functions are linked, so you can get there directly with one click.
From simulation to production:
Component Manager Configure robot system
Robot Simulator Simulate production processes
Scenario Designer The whole plant in 3D
Builder Create robot program
Operator Cockpit Control and monitor production
More functions:
Operator Panel The digital teach counterpart
Wizards Parameterize function blocks
Custom Wizard Program Templates
User Management Admin, Technician, Operator
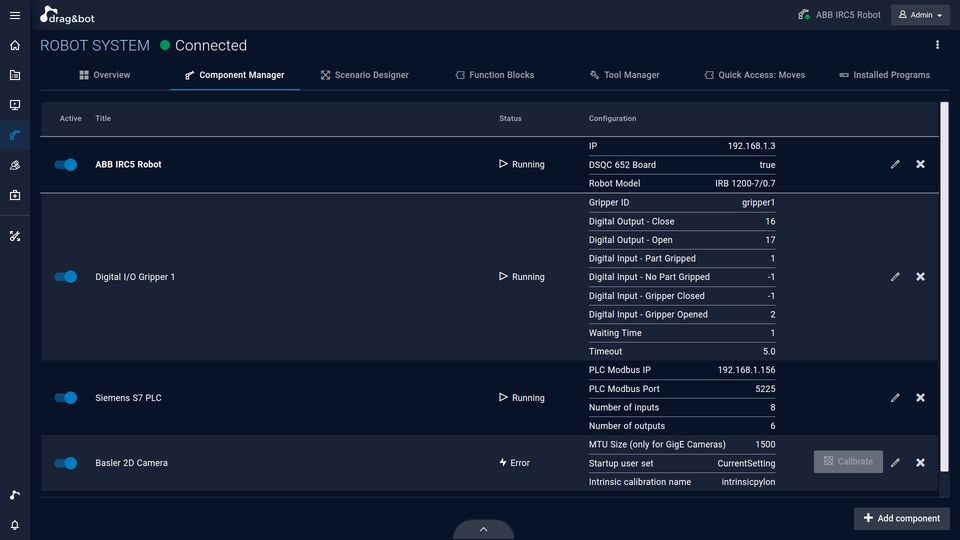
1. Component Manager
Configure robot system
The user configures the connected hardware in the Component Manager. The installation of the corresponding drivers for the hardware takes place fully automatically in the background. Subsequently, the desired function blocks for the corresponding hardware can be loaded. For certain hardware, a configuration for communication with drag&bot is also necessary.
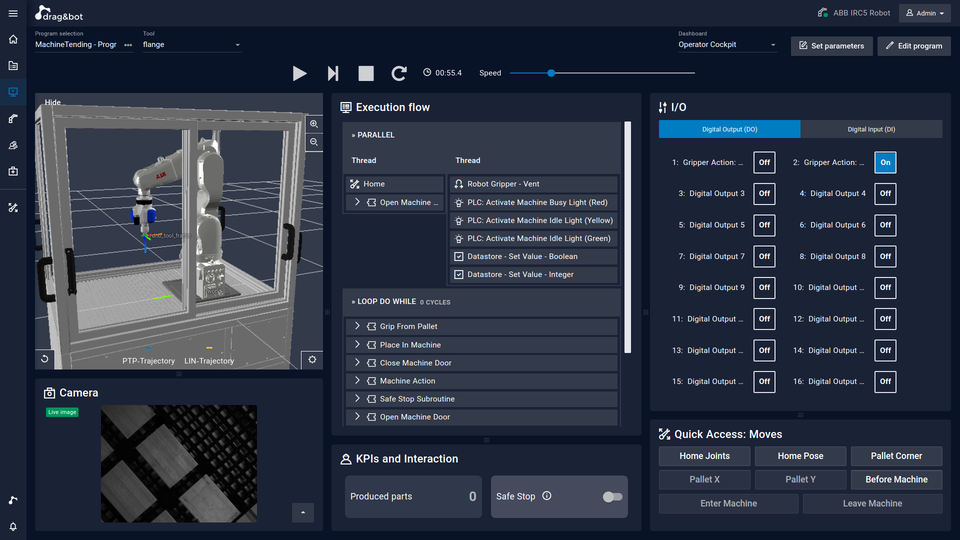
2. Robot Simulator
Simulate production processes
The simulated robot in drag&bot can be used with any robot arm (different manufacturers and sizes available). This allows users to quickly and easily simulate the process to be automated without the need for physical hardware. The result can be used as a basis for automation decisions in terms of technical feasibility (e.g. reachabilities and rough cycle time estimates).
3. Scenario Designer
The whole plant in 3D
In the 3D environment of Scenario Designer, users can import their own CAD models and combine them with 3D models of robots, grippers and cell designs. Scenario Designer makes it possible to change the size, position and orientation of objects and create digital images of the plant. The scenario can then be saved for later reuse. For easy access to this function, already configured scenarios are available for free editing.
4. Builder
Create robot program
In the drag&bot Builder, applications can be created from predefined function blocks via drag & drop. drag&bot already contains all function blocks required for common robot applications, e.g.:
-
Move robot
-
Open and close gripper
-
Set and read I/Os
-
Palletize
-
Loops, branches, parallel execution
-
Wait, abort program, ...
5. Operator Cockpit
Control and monitor production
Programs are executed and monitored with the Operator Cockpit. The freely configurable HMI can be adapted to the requirements of the application and the operator. Contents of the cockpit can be, for example, live camera images, grid management, sensor data, production data or interaction surfaces. The cockpit also offers useful functions for setters or maintenance staff: With one click, they are back in the Builder and can expand and optimize the application.
Wizards
Parameterize function blocks
Wizards are graphical operating and input aids. They help to configure the settings required for some function blocks via a graphical user interface. Users can thus adapt function blocks to the specific requirements of their application without expert knowledge. The following wizards are part of drag&bot CORE:
Functions:
- Move robots and save positions
- Create robot paths from single positions
- Define grid of a magazine for part pickup/retrieval
- Define finger position, closing force and closing speed of grippers
Custom Wizard
Program Templates
Custom wizards guide the user step-by-step through the creation of a program flow for a specific use case.
Example Grid Wizard:
At the beginning, the basic grid shape is selected, followed by the number of rows and columns. The robot must be moved to three corners of the grid so that the coordinates of the grid in space and those of the individual fields can be determined. In the final steps, the program logic and gripping strategies are determined. The result is an immediately executable drag&bot program.
User Management
Admin, Technician, Operator
The functions available to a user depend on the role that the administrator has assigned to him. The administrator of a system can create, modify or delete users. The three available roles are: Admin, Technician, Operator. The operator, for example, only has access to an operator cockpit configured for him as well as released programs.
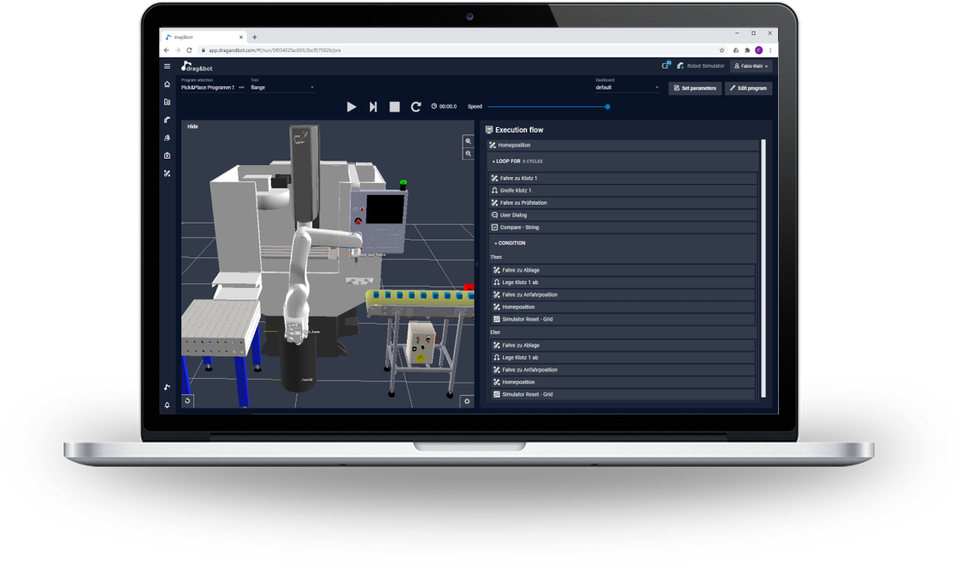
drag&bot SIMULATION
Try out the software yourself
drag&bot SIMULATION is the test version of drag&bot OS that works completely in your browser in the cloud without real robot hardware. Sign up right now to get to know our software - and receive your personal access data directly via email so you can get started right away.