
Basic components
Modular construction kit of hardware and software
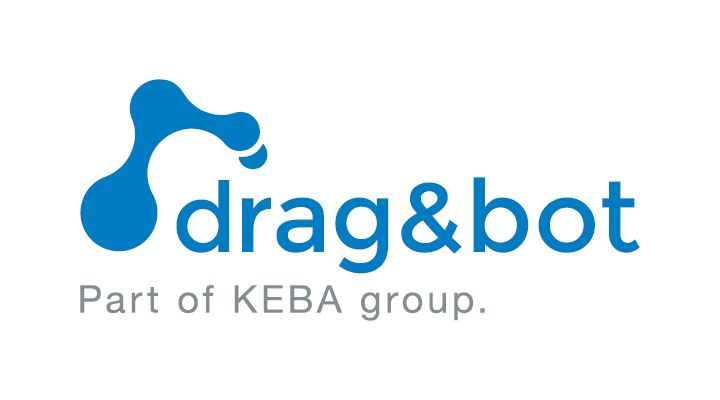
Software
drag&bot OS is a software for intuitive, graphical simulation, commissioning, programming and operation of robot applications.
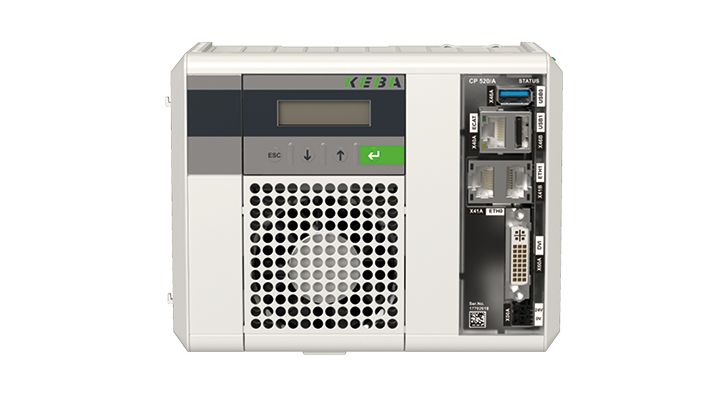
Control
The software is run on a powerful control system from KEBA. In addition, the Kemro X control platform offers many more options.
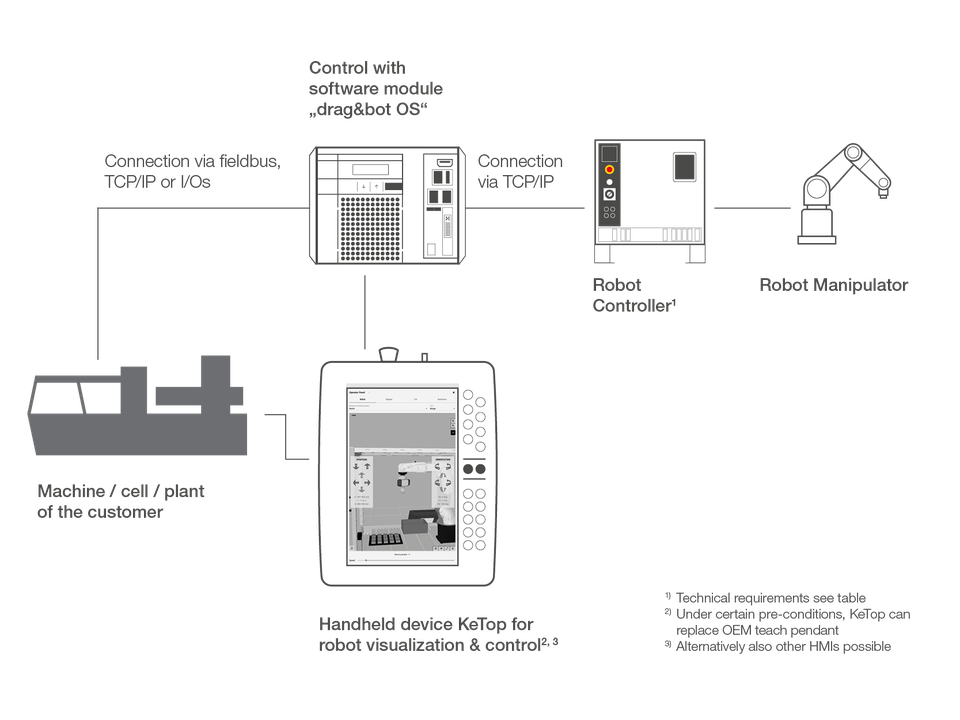
Typical system architecture
For integration of drag&bot OS into machines and robot solutions.
-
drag&bot OS runs on a control system from KEBA.
-
The connection of the customer's machine can be made via a local network connection (TCP/IP), digital input/output signals or fieldbus interfaces (e.g. EtherCAT).
-
The communication with the 3rd party robot controller (e.g. KUKA, ABB or Fanuc) is done via TCP/IP - for more information about supported brands and models see Hardware interfaces.
-
For operation and visualization, a KeTop handheld terminal can be used. Alternatively, the display and use of the software is also possible via network using a browser or as part of an existing visualization (e.g. using the iFrame technology).
Modular control
The drag&bot OS software is alternatively available as a module in Kemro X - the modular control platform from KEBA. The combination of Kemro X and drag&bot OS results in further advantages. For example, the following functions can be used together with drag&bot OS on a KEBA control:
Individual machine visualization
Using KEBA's own visualization framework, machine builders can quickly and efficiently create their own graphical user interfaces.
Own robot control
KeMotion, the robot control software from KEBA is compatible with drag&bot OS and can be used together.
Interfaces & Hardware Modules
Kemro X has its own EtherCAT master and also supports other industrial protocols. In addition, various interfaces are available.
Integrated SPS
Kemro X uses CODESYS for SPS programming for industrial control and automation technology.
Choose a topic
- Technical Questions
- Alternatives
- Service & Support
- Technical Questions
- Alternatives
- Service & Support
Top 5 questions and answers
Here we have listed the most important questions & answers from our FAQ section for you.
More detailed info and further answers can be found in the related topics.
1
Can I control more than one robot with drag&bot OS?
A software license allows the control of one robot at a time. Within the software, the robot model can be changed at any time. However, multiple software instances of drag&bot OS can communicate with each other and thus enable complex multi-robot applications.
2
Can I install the software on my own hardware?
To simplify the installation of drag&bot OS, our software is always delivered together with a powerful control from KEBA. In series use (> 50 licenses/year), the installation of the software on other, powerful hardware is conceivable.
3
Are there interfaces to Profibus or EtherCAT? Is drag&bot OS real-time capable?
Yes, drag&bot OS - in combination with Kemro X - offers interfaces to various industrial communication protocols, including Profibus and EtherCAT. drag&bot OS itself, however, is web-based and thus not real-time capable.
4
Who provides training and support for the software or the overall system?
End users, research & development users and educational institutions receive the software together with individual training and on-site support directly from our partners .
Machine builders and robot manufacturers with series production as well as system integrators are supported directly by us and are welcome to contact us for this purpose.
5
What is the drag&bot business model?
drag&bot OS is sold as a one-time runtime license together with a CP520 KEBA controller and further accessories.
For machine builders, system integrators and robot manufacturers in series production, the transaction is handled by KEBA Industrial Automation Germany GmbH or KEBA Group AG from Linz.
For other customer groups, such as manufacturing end users, users from the area of research & development and educational institutions, processing takes place via our partners.
How much effort is required to set up a robot with drag&bot OS?
Depending on the robot brand, setting up a robot for drag&bot OS takes between 30 and 120 minutes. Details can be found in our online documentation.
Which robots and other hardware are supported?
drag&bot OS supports a wide range of robots, including industrial robots from manufacturers such as ABB, Fanuc, KUKA, Yaskawa, Nachi, Epson, Stäubli, Denso, Mecademic, Universal Robots. The software supports all common grippers and various cameras and vision systems.
For more information see hardware interfaces - Supported Hardware.
Can I control more than one robot with drag&bot OS?
A software license allows the control of one robot at a time. Within the software, the robot model can be changed at any time. However, multiple software instances of drag&bot OS can communicate with each other and thus enable complex multi-robot applications.
Can I install the software on my own hardware?
To simplify the installation of drag&bot OS, our software is always delivered together with a powerful control from KEBA. In series use (> 50 licenses/year), the installation of the software on other, powerful hardware is conceivable.
Are there interfaces to Profibus or EtherCAT? Is drag&bot OS real-time capable?
Yes, drag&bot OS - in combination with Kemro X - offers interfaces to various industrial communication protocols, including Profibus and EtherCAT. drag&bot OS itself, however, is web-based and thus not real-time capable.
Can the robot follow a given path with drag&bot OS?
It is currently not possible to take over a path from a 3D model directly as a trajectory in
drag&bot OS. However, this can be developed individually for the customer
Potential, this can be developed individually for the customer.
How does drag&bot OS communicate with PLC controllers?
drag&bot OS communicates with the PLC from KEBA - the Kemro X control platform - directly via the internal variable server.
For data exchange with other PLC systems - such as a Siemens S7 - communication via TCP/Modbus is possible.
Does drag&bot OS run on every KEBA controller or every KeTop?
drag&bot OS works with all KEBA controllers of the models CP520, DU365 or better, whereby an additional 40 GB CFlash Card is required. Currently, only the KeTop T150-r10-AN0-Lx is supported for operation via KEBA manual control unit. With corresponding potential, other hardware is also conceivable within the scope of a development project.
How can I take advantage of Kemro X in connection with drag&bot OS?
The easiest way to use drag&bot OS without Kemro X is to load it via an image on a suitable KEBA controller.
If you also want to use the advantages of Kemro X in drag&bot OS, you first have to create a new project via the KeStudio software and add drag&bot OS as a module to the project. Afterwards a common data storage, the so called variable server, can be used to connect Kemro X and drag&bot OS between Kemro X and drag&bot.
Does the KeTop hand control panel replace the original teach pendant of the robot manufacturer?
The easiest way to use drag&bot OS without Kemro X is to load it via an image onto a suitable KEBA controller.
If you want to use the advantages of Kemro X for the setup of the robot (calibration, safety areas, etc.), the original teach-pedant of the robot manufacturer is required. For selected robot brands, such as Nachi, safe teach-in in the robot workspace is also possible via the KeTop alone, so that for many cases, the end user can operate the robot via the KeTop alone.
Can you also work with robot XYZ?
An overview of already integrated robots and corresponding robot controllers can be found under Hardware overview.
If your desired robot manufacturer or controller is not included, please contact us to clarify whether an integration is possible.
Does drag&bot OS support the gripper/tool XYZ?
An overview of supported grippers, cameras and tools can be found on our hardware interfaces page.
Is it possible to transfer the native robot code of an existing robot from e.g. ABB or Fanuc into drag&bot OS?
No, this is currently not possible. But robot programs can be created quickly in
drag&bot OS.
What advantages does the software have over collaborating robots (=cobots)?
Compared to cobots, drag&bot OS offers a platform-independent solution that unifies the operation of different robot manufacturers. It also offers easier programming, a dynamic dashboard for the worker that can be adapted to the application, and in combination with Kemro X, an integrated PLC control and other software modules.
How does drag&bot OS differ from other robotics software solutions on the market?
Our software is characterized by its particularly user-friendly, graphical, no-code user interface for workers and end users, which significantly simplifies the simulation, setup and operation of robot applications. Unlike other solutions, we support a very wide range of different robot brands and offer open interfaces based on ROS1 for manufacturers to develop their own drivers for peripheral devices.
What is the drag&bot business model?
drag&bot OS is sold as a one-time runtime license together with a CP520 KEBA controller and further accessories.
For machine builders, system integrators and robot manufacturers in series production, the transaction is handled by KEBA Industrial Automation Germany GmbH or KEBA Group AG from Linz.
For other customer groups, such as manufacturing end users, users from the area of research & development and educational institutions, processing takes place via our partners.
How much does the software cost?
The drag&bot OS runtime license together with a CP520 KEBA controller and other accessories has a current end customer list price of € 4.990.00. The KEBA handheld control unit with accessories currently costs € 3.870.00 in the end customer list price (prices subject to change as of 11/2023).
How and where can I get a quote for the software or solution packages?
Machine builders and robot manufacturers with series production please contact us or KEBA directly via our contact form .
End users, users from the area of research & development and educational institutions please contact our partners directly for offers and further information.
Does drag&bot deliver a finished robot application?
Drag and bot GmbH exclusively develops and distributes software. In addition, we develop individual solutions for series use for robot manufacturers and machine builders as part of development projects.
We also offer our end customers robot programming services or ready-to-use turn-key solutions based on drag&bot OS via our partners.
Who provides training and support for the software or the overall system?
End users, research & development users and educational institutions receive the software together with individual training and on-site support directly from our partners .
Machine builders and robot manufacturers with series production as well as system integrators are supported directly by us and are welcome to contact us for this purpose.
Step by Step to your success
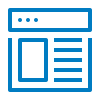
1 Software Test
Simply register for drag&bot SIMULATION and test drag&bot yourself for free directly in your browser.
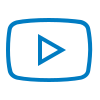
2 Web Demo
We will show you the most important functions of drag&bot OS and answer your questions about your series application.
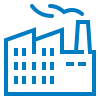
3 Individual Consulting
Our team from KEBA advise you personally on your series application or machine concept.
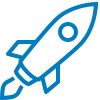
4 System Integration
You order a test system and we help with setup and support during the machine implementation.