Mit minimalem Aufwand ist Ihre Hardware mit drag&bot OS verbunden
drag&bot OS unterstützt eine Vielzahl unterschiedlicher Roboter, nahezu alle Greifer und Material-Zuführsysteme sowie die gängigsten Bildverarbeitungssysteme und Kommunikationsschnittstellen.
Sparen Sie wertvolle Zeit bei der Integration von Greifern, Kameras oder SPS-Systemen. Mit minimalem Aufwand ist Ihre Hardware mit drag&bot verbunden und Sie können sofort loslegen.
Verwenden Sie die Hardware, die am besten zu Ihrer Anwendung passt!
Roboter
Roboter Hersteller | Controller & Software-Versionen | Benötigte Software-Pakete vom Roboter-Hersteller |
---|---|---|
ABB | IRC5,IRC5 Compact, Omnicore | 616-1 PC Interface 623-1 Multitasking |
Fanuc | R-30iB Mate & Plus > V8.10 (not V8.33) | R648 User Socket Msg R632 KAREL |
KUKA | KR C4 iiwa | RSI > 3.1.6 Sunrise > 1.13 |
Yaskawa | YRC1000 | MotoPlus |
Stäubli | CS9 | - |
Nachi | CFD >4.72 | - |
Comau | KEBA KeMotion | See Kemro X Licences |
Epson | SPEL 7.0+ | - |
Denso | RC8: VS087 | b-CAP (Teil von ORiN2 SDK) |
Mecademic | Meca500 R3 | - |
Universal Robots | CB2, CB3, e-series | - |
Greifer
drag&bot OS unterstützt eine Vielzahl unterschiedlicher Greifer und Greifsysteme verschiedener Hersteller:
Zimmer
Die Zimmer Group liefert sowohl einbaufertige Klemmgreifer als auch kundenspezifische Roboterlösungen zum Greifen und Positionieren. Unterstützt werden alle Greifer auf IO Basis. Für Greifer, die das IO-Link Protokoll nutzen, wird zusätzlich ein IO-Link Master Adapter benötigt.
Schmalz
Marktführer in der Automatisierung mit Vakuum. Unterstützt werden alle IO-basierten Greifysyteme, z. B. die ECBPi oder FXCB Serie.
Schunk
Schunk ist weltweit die Nr. 1 bei industriellen Greifsystemen. Unterstützt werden alle IO Greifer sowie alle Greifer der WSG-Serie.
Robotiq
Robotiq bietet diverse Greifer, Bildverarbeitungssysteme und Sensoren für Cobots. Unterstützt werden neben den IO-Greifern auch die Modbus basierten Modelle 2F-85 und 2F-140.
Weiss Robotics
Weiss Robotics bietet u.a. digitale Klemmgreifer und UR+ zertifizierte Greiflösungen. Unterstützt werden die WSG-Modelle des Herstellers.
Kamerasysteme
drag&bot OS unterstützt eine Reihe unterschiedlicher 2D- und 3D-Bildverarbeitungssysteme:
Basler
Basler bietet eine große Bandbreite günstiger USB und Netzwerk Kameras und Zubehör für die Industrie.
Balluff
Balluf´s Smart Vision Smartcams eignen sich besonders zum schnellen Einsatz bei Fehlererkennung und Qualitätsprüfung.
Cognex
Cognex´s Insight Smartcams decken eine breite Palette von Anwendungen ab und sind mit umfassendem Zubehör (Linsen, Licht, etc.) verfügbar.
Roboception
Roboception bietet günstige 3D Smartcams und Software Module für spezifische Anwendungen in der industriellen Automation.
Schnittstellen
Die Software drag&bot OS ist alternativ als Modul in Kemro X - der modularen Steuerungsplattform von KEBA - verfügbar. Durch die Kombination aus Kemro X und drag&bot OS ergeben sich weitere Vorteile. So können beispielsweise die folgenden Funktionen gemeinsam mit drag&bot OS auf einer KEBA-Steuerung genutzt werden:
Individuelle Maschinen-Visualisierung
Mit Hilfe des KEBA eigenen Visualisierungsframeworks können Maschinenbauer schnell und effizient ihre eigenen graphischen Benutzeroberflächen erstellen.
Eigene Roboter-Steuerung
KeMotion, die Roboter-Steuerungssoftware von KEBA, ist kompatibel zu drag&bot OS und kann zusammen genutzt werden.
Schnittstellen & Hardware Module
Kemro X verfügt über einen eigenen EtherCAT Master und unterstützt auch andere Industrieprotokolle. Zudem sind diverse
Schnittstellen verfügbar.
Integrierte SPS
Kemro X nutzt CODESYS zur SPS Programmierung für die industrielle Steuerungs- und Automatisierungstechnik.
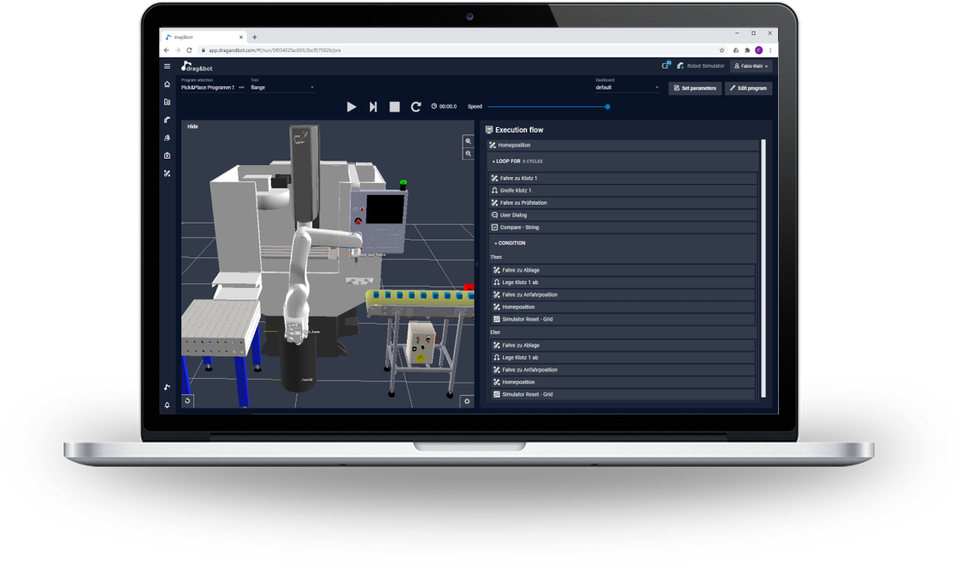
drag&bot SIMULATION
Software selbst ausprobieren
drag&bot SIMULATION ist die Testversion von dra&bot OS, die vollständig in Ihrem Browser bzw. in der Cloud (ohne echte Roboter-Hardware) funktioniert. Melden Sie sich gleich an, um unsere Software kennenzulernen – und erhalten Sie direkt Ihre persönlichen Zugangsdaten per E-Mail, damit Sie sofort loslegen können.
Ihre Möglichkeiten sofort loszulegen
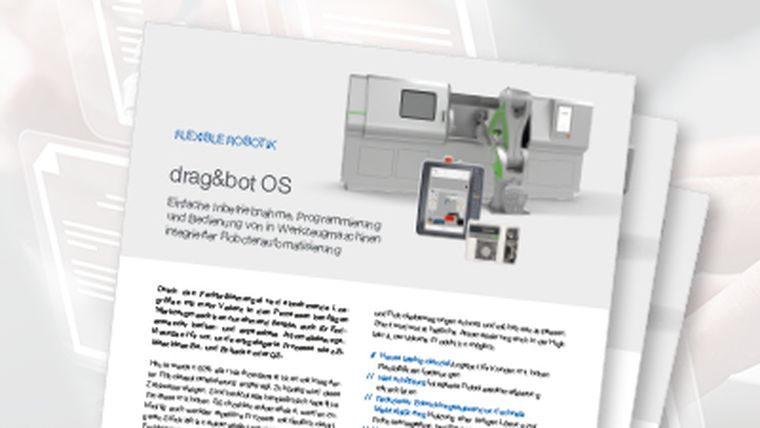
Datenblatt herunterladen
Lesen Sie das drag&bot OS Datenblatt zur integrierten Roboterbedienung bei Maschinen.
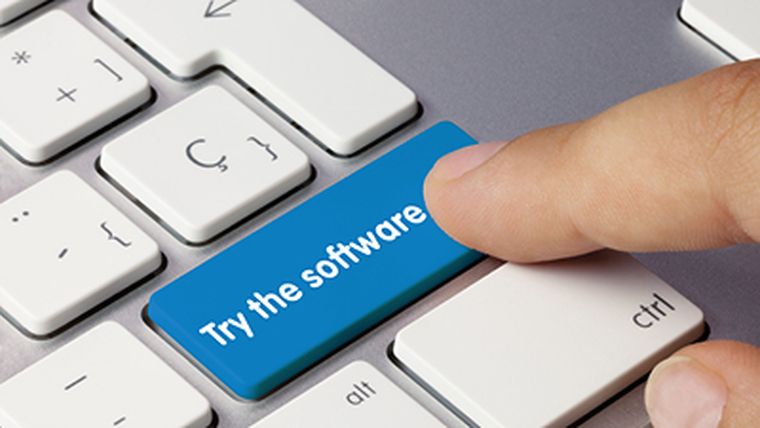
Software kostenlos testen
Testen Sie jetzt drag&bot SIMULATION - ganz ohne Roboterhardware direkt im Browser.